In the realm of heavy industry, especially mining, mineral processing, and chemical plants, equipment downtime can have significant financial and operational repercussions. CNSME Pump recognizes the critical importance of maintaining continuous operations through easy access to spare parts. Their comprehensive spare parts availability for all centrifugal slurry pump models not only ensures that industries can minimize downtime but also reinforces trust and reliability in their products. This commitment reflects a customer-centric approach, emphasizing quick response times, high-quality components, and extensive inventory, making CNSME a trusted partner for industries worldwide.
Extensive Range of Spare Parts for Every Model
CNSME Pump offers an extensive inventory of spare parts compatible with all their centrifugal slurry pump models. Whether it is impellers, liners, shafts, seals, or bases, they ensure that replacement parts are readily available to meet a wide variety of operational needs. This vast range covers both common standard parts and specialized components tailored for unique applications. The availability of such a comprehensive catalog allows operators to stock strategically, ensuring that critical components are on hand before wear or unforeseen failures occur, thereby preventing costly production halts. The company’s inventory management system is designed to quickly identify and dispatch the necessary parts efficiently.
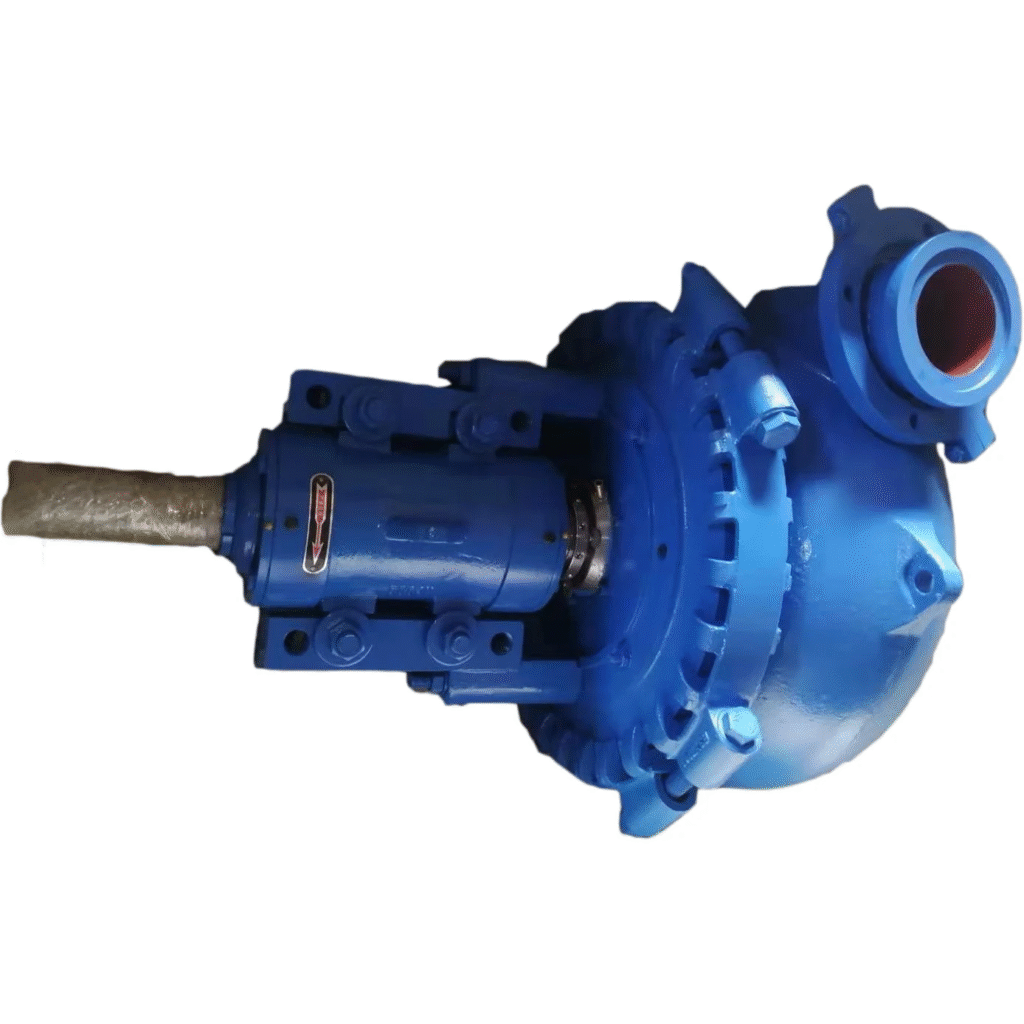
Quality Assurance to Match Original Equipment Standards
Not all spare parts are created equal, and CNSME Pump places great emphasis on maintaining high standards in every component they supply. All spare parts are manufactured using rigorous quality control procedures, ensuring they meet or exceed original equipment manufacturer (OEM) standards. This commitment to quality guarantees that replacement components fit perfectly, function reliably, and withstand the harsh operating conditions typical to slurry handling environments. Whether sourcing parts locally or internationally, clients can trust that CNSME’s spare parts will preserve the integrity of their pumps and maintain optimal performance over extended service periods.
Fast Delivery and Global Logistics Support
Time is often of the essence when a critical pump part fails unexpectedly. CNSME Pump has established an efficient logistics network to facilitate quick delivery of spare parts to customers worldwide. They work with trusted logistics partners to ensure that parts are dispatched promptly, minimizing downtime regardless of geographic location. Their global reach, combined with local warehouses and regional distribution centers, enables rapid response and delivery times. This level of logistical support helps industries avoid prolonged shutdowns, safeguarding production schedules, and maintaining operational continuity.
Custom and Hard-to-Find Parts Solutions
In complex industrial environments, sometimes standard spare parts are insufficient, and specialized or custom components are required. CNSME Pump understands these needs and offers bespoke solutions for hard-to-find or customized parts. Their R&D team works closely with clients to produce replacement parts that perfectly match the OEM specifications or meet custom design requirements. This flexibility ensures that even unique or legacy pump models are supported with suitable spare parts, extending their operational life and reducing the need for expensive equipment replacements. CNSME’s commitment to supplying hard-to-find parts embodies their dedication to comprehensive customer service.
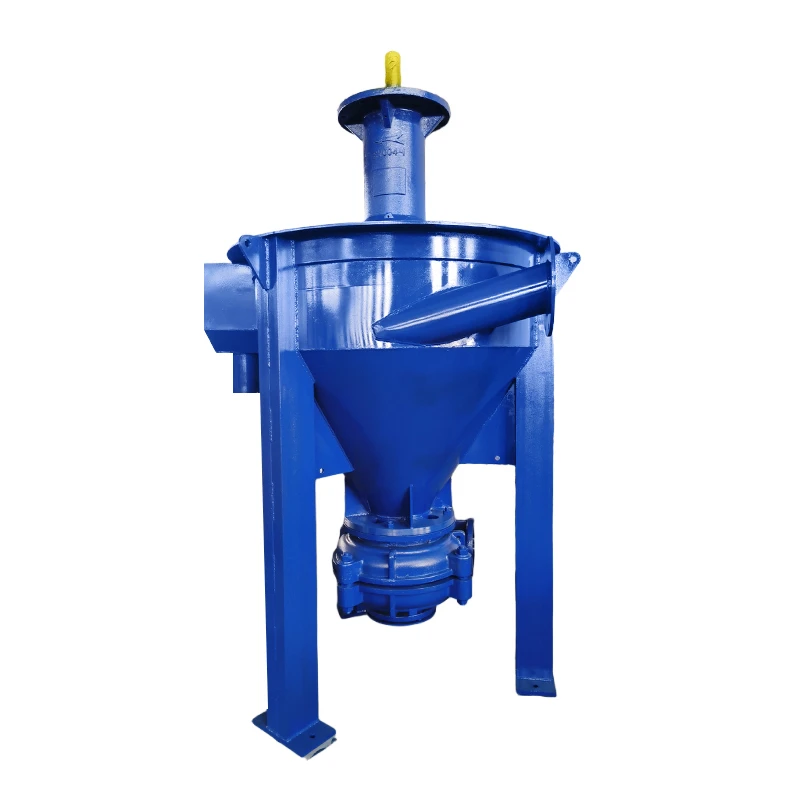
Cost-Effective Spare Parts Management
Maintaining a large inventory of spare parts can seem costly, but CNSME Pump advocates for a strategic approach that balances cost and availability. By offering quality parts at competitive prices and providing expert advice on inventory management, the company helps clients reduce unnecessary stockpiling while ensuring essential components are accessible. Their technical support team assists in developing tailored spare parts strategies aligned with operational demands, asset management practices, and budget constraints. Such proactive planning allows industries to optimize maintenance schedules, cut costs, and improve overall equipment effectiveness without compromising on reliability.
Ongoing Support and Technical Assistance
Beyond just supplying spare parts, CNSME Pump provides ongoing technical support to ensure proper replacement, installation, and maintenance. Their experienced technical team offers guidance on parts compatibility, installation procedures, and troubleshooting, which helps prevent installation errors or premature failures. Additionally, CNSME often provides training sessions for maintenance personnel to ensure they are familiar with the specifications and best practices associated with parts replacement and upkeep. This holistic approach ensures that spare parts are utilized effectively, maximizing their lifespan, and sustaining the overall health of the pumping systems.
Conclusion
CNSME Pump’s commitment to spare parts availability for all centrifugal slurry pump models demonstrates their dedication to supporting customer success through reliable, timely, and high-quality supply chain solutions. Their extensive inventory, quality assurance processes, fast global logistics, and flexible solutions for custom and hard-to-find parts collectively cater to the urgent needs of industries where downtime is costly. Coupled with ongoing technical support, CNSME ensures that clients can maintain optimal pump performance, extend equipment life, and operate with confidence in even the most challenging environments. As industries evolve, CNSME’s emphasis on spare parts logistics and comprehensive service will continue to be a vital pillar in their reputation as a dependable equipment provider.