In the fast-paced world of automotive manufacturing, precision and efficiency are key to staying ahead of competition. Custom tooling plays a vital role in this landscape by enabling the production of high-quality injection molds and prototypes tailored specifically to the needs of automakers. These custom tools allow manufacturers to develop complex, functional, and visually appealing parts with tight tolerances, ensuring that each component meets strict industry standards. Whether for small batch runs, rapid prototyping, or full-scale production, customized tooling solutions are fundamental in turning innovative automotive concepts into reality, offering both flexibility and reliability in the manufacturing process.
The Importance of Custom Tooling in Automotive Manufacturing
Custom tooling is the backbone of producing automotive parts that demand intricate design features, consistent quality, and perfect fit. Unlike standard molds, which are designed for mass production of generic parts, custom tools are engineered to cater to specific project requirements, whether that involves complex geometries, unique surface textures, or multi-material applications. These tools are crucial for ensuring design fidelity, reducing waste, and minimizing cycle times. They also facilitate quick modifications and iterations, which are especially important in the prototyping phase. In essence, custom tooling provides automakers with the flexibility to innovate, streamline their production workflows, and ultimately deliver superior products to market.
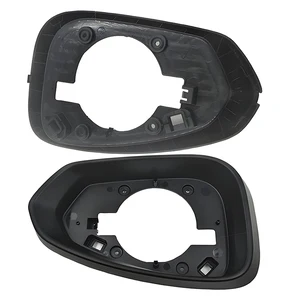
Innovations in Tool Design and Manufacturing
The creation of custom automotive tooling has benefited immensely from technological advancements in design and manufacturing. Modern computer-aided design (CAD) and simulation software enable engineers to develop highly detailed, optimized molds before even manufacturing the physical tool. This reduces errors, shortens lead times, and improves the overall quality of the final product. Manufacturing techniques such as high-precision CNC machining, EDM (Electrical Discharge Machining), and additive manufacturing are now common in creating complex mold components with exact specifications. These innovations allow for faster turnaround times, greater flexibility in design adjustments, and highly durable tools capable of withstanding the demanding conditions of automotive production, ensuring consistent quality throughout the life of the mold.
Material Selection and Durability of Custom Tools
Choosing the right materials for custom molds is critical for ensuring longevity and performance. Automotive injection molds often require robust materials like hardened steel, carbide inserts, or high-strength alloys that provide resistance to wear, heat, and chemical corrosion. These materials are selected based on factors such as part complexity, production volume, and required surface finish. The durability of the tooling directly impacts the consistency and quality of each batch, reducing downtime for repairs or refurbishments. Furthermore, surface treatments like coatings and polishing are applied to enhance wear resistance and surface quality, facilitating the production of high-finish parts with fine details. High-quality materials combined with precise manufacturing processes extend the lifespan of molds, ultimately saving costs and maximizing productivity.
The Role of Prototyping and Small Batch Runs
Prototyping with custom tooling is a vital step in the development of new automotive parts. It allows manufacturers to evaluate design functionality, aesthetic details, and fit before committing to full-scale production. Custom tools enable rapid creation of prototypes, providing instant feedback on potential issues and design improvements. Small batch runs made with bespoke tooling help identify manufacturing challenges early on, reducing costly revisions later in the process. This iterative approach fosters innovation, allowing designers to refine features, test new materials, and ensure compliance with safety standards. By investing in custom tooling for prototypes, automotive companies can significantly cut time-to-market and improve overall product quality, ensuring that final production parts perform flawlessly.
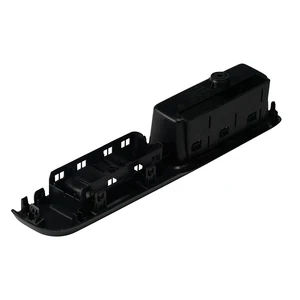
Future Trends in Custom Tooling and Innovation
The future of custom tooling for automotive injection molds is poised to be shaped by increasingly integrated and intelligent manufacturing solutions. Adaptive tooling systems equipped with sensors and automation will enable real-time monitoring of key parameters such as temperature, pressure, and wear, leading to predictive maintenance and minimized downtime. Advances in additive manufacturing will allow for even more complex, lightweight, and highly tailored mold components, reducing lead times and costs associated with traditional machining methods. Furthermore, multi-material tooling will expand the ability to produce parts with diverse finishes and properties within a single mold setup. As sustainability becomes more essential, eco-friendly materials and processes are being developed to reduce waste and energy consumption. These innovations will empower automotive brands to quickly adapt to evolving consumer demands, deliver higher quality, and reduce their environmental footprint.
Collaborating with Experts in Custom Tooling
Partnering with experienced and innovative tooling suppliers is vital for automakers aiming to leverage the full potential of custom molds and prototypes. Trusted partners bring extensive expertise in design, material science, and manufacturing, ensuring that every tool is optimized for its specific application. They understand the nuances of automotive parts production and can recommend solutions that balance cost, quality, and speed. Close collaboration during the design phase helps incorporate features that facilitate maintenance, ease of assembly, and future modifications. Ongoing support during production, including mold maintenance and refurbishment, ensures consistent performance and longevity.