In the competitive landscape of household products, original equipment manufacturers (OEMs) are turning to advanced tooling solutions to stay ahead of market demands. A reliable OEM houseware mold manufacturer equipped with cutting-edge tooling capabilities can produce high-quality, durable, and innovative products that resonate with consumers’ evolving preferences. The importance of such manufacturers goes beyond simple production; they act as strategic partners who can influence product success through their expertise, technological capabilities, and commitment to quality. This article explores the key aspects of OEM houseware mold manufacturing, emphasizing advanced tooling techniques, innovation, quality assurance, and the long-term benefits of working with a forward-thinking partner.
The Role of Advanced Tooling in OEM Houseware Manufacturing
At the core of producing household items that combine functionality and aesthetic appeal lies the use of advanced tooling. High-quality molds are essential for producing parts with precise dimensions, smooth surfaces, and consistent quality. Advanced tooling involves employing sophisticated CAD/CAM systems for detailed mold design, as well as precision manufacturing processes like high-speed CNC machining, electrical discharge machining (EDM), and laser deburring techniques. These technologies enable OEM mold manufacturers to create complex cavity geometries and intricate surface textures that elevate the look and feel of household products. The increased precision achievable through advanced tooling also reduces defects, minimizes waste, and improves overall manufacturing efficiency. In this competitive arena, leveraging state-of-the-art tooling techniques can make the difference between an ordinary product and a premium household item that stands out in the marketplace.
Customization and Engaging Design Solutions
OEM houseware mold manufacturers with advanced tooling capabilities are uniquely positioned to offer highly customized solutions tailored to client specifications. Whether a brand wants ergonomic handles, textured surfaces for better grip, or decorative patterns that highlight branding, advanced tooling enables rapid adaptation and innovation. The flexibility of such tooling also facilitates rapid prototyping, allowing brands to quickly test and refine their designs before mass production. The ability to incorporate multi-material inserts, soft-touch surfaces, or integrated logos directly into molds offers significant aesthetic and functional advantages. Customized tooling solutions not only meet specific market demands but also help brands carve out a distinct identity, adding value that resonates with consumers and boosts market appeal.
Quality Assurance through Precision and Technology
Ensuring consistent product quality is non-negotiable for OEM houseware injection mold Advanced tooling significantly bolsters quality assurance by enabling tighter tolerances, better surface finishes, and defect-free parts. Modern manufacturing technologies, such as multi-axis CNC machines, combined with in-process inspection techniques like 3D scanning and coordinate measuring machines, help detect and correct deviations early. Regular mold maintenance and real-time monitoring during production prevent issues like wear, warping, or misalignments that could compromise product quality over time. Partnering with an OEM mold manufacturer that prioritizes precision and employs rigorous quality checks ensures that every household item produced adheres to exact specifications. This consistency reduces the risk of warranty claims, recalls, or customer dissatisfaction, enabling brands to build trust and loyalty with their consumers.
Rapid Development and Production Scalability
One of the most critical advantages of working with an OEM houseware mold manufacturer equipped with advanced tooling is the ability to accelerate development cycles. Rapid prototyping through 3D printing or quick-turn CNC machining allows brands to test molds and refine designs in a fraction of the traditional time. Once validated, these advanced molds can support high-volume production with minimal cycle times, making it feasible to meet tight schedules and market windows. The scalability of such molds ensures that manufacturers can scale production up or down based on demand without sacrificing quality or lead times. This agility is crucial for brands seeking to launch new products swiftly, respond to seasonal trends, or manage inventory efficiently without the risk of delays or quality issues.
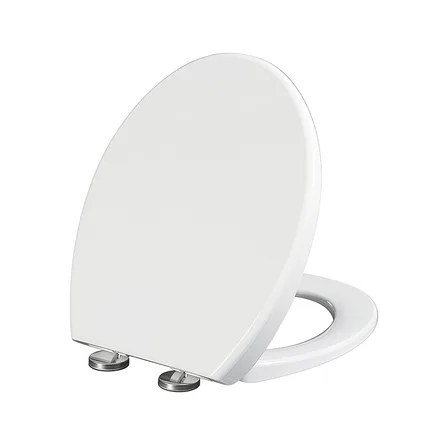
Long-term Cost Savings and Durability
Investing in advanced tooling and OEM partnerships results in significant long-term benefits. High-end molds designed and manufactured using innovative techniques offer greater durability, enabling thousands or even millions of injection cycles without needing frequent repairs or replacements. This longevity reduces replacement costs and minimizes downtime, ensuring a steady supply of household products. Additionally, precise molds lead to fewer defective parts, reducing material scrap and rework costs. The overall efficiency gained through advanced tooling techniques translates into lower production costs over the lifespan of the mold, making it an economical choice for brands aiming for both quality and cost-effectiveness. This combination of durability, efficiency, and reduced waste underscores the strategic value of partnering with a forward-looking OEM houseware mold manufacturer.
Supporting Innovation and Future Growth
Advanced tooling capabilities empower OEM houseware manufacturers to support ongoing innovation and product diversification. As consumer preferences shift towards more sustainable, ergonomic, and smart household items, molds must evolve to accommodate new materials, complex geometries, and integrated features. Tooling innovations such as conformal cooling channels, hot runner systems, and multi-material inserts enable manufacturers to develop advanced products that meet today’s high standards. By continuously investing in new technologies, OEM partners stay ahead.